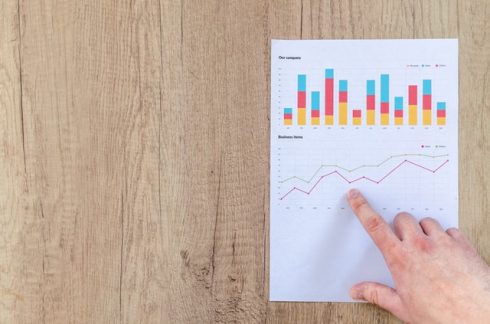
Value Stream Management is a way to manage what your organization is doing to ensure you’re optimizing business value while eliminating costly waste from your development and delivery processes. It’s part of today’s digital transformation.
“Right now, everybody’s in this digital disruption,” said Lance Knight, SVP and GM at Value Stream integration provider ConnectALL. “How important was it 30 years ago, that IT worked right? It was kind of important, but today it’s paramount. CIOs are now getting a seat at the table. They’re differentiators.”
RELATED CONTENT:
The realities of value stream management
A guide to VSM tools
Gently down the value stream
To gain efficiencies and deliver greater value, you have to first see how your organization is functioning. And the only way to assess that is through the use of data. But what data?
Today, most organizations use measurements, metrics and KPIs to gain efficiencies in how they work, with one of the critical outcomes being IT predictability. Organizations can make better decisions about embarking on strategic initiatives and the time it will take to implement if they know that IT is predictable. But Knight argues that many of those companies are getting it wrong.
“If I don’t have predictable IT to deliver, and I can’t get predictable until I have metrics, and I’m not going to get metrics until I have the right measurements, that’s where value stream starts to play,” he said. “That’s where the true impact comes in at the higher levels.”
Measurements, Knight explained, are snapshots in time. It tells you how long it took you to do one thing once. Metrics and KPIs are the averaging of repeated measurements over time. A KPI (key performance indicator) is what organizations use to gauge their success — organizationally, departmentally, by project and by team.
Using an example from industry, Knight said: “Let’s say a defect comes in and it takes 10 days to fix that defect and deploy it into production. That just tells me it took 10 days for that one defect fix. What amplifies the issue is everything that comes into the system of delivery are of different sizes. It’s always going to be a different measurement. It’s considering the time to fix a defect in aggregate that makes me more predictable, not that one time it took me to fix the defect. It’s the variance and 80 percentile that are useful. Those are the metrics to me. The measures are just that, individual measurements.”
“Then,” he continued, “I can use that 80th percentile of completion time, or the KPI, to inform my efforts to become more predictable. Using appropriate metrics helps me take into account all the different sizes of work that go through my system. But nobody’s talking about that; they’re talking about the measurement.”
Once you have the metrics, you can see the impact of your organizational efforts on delivering value, and you can take action based on a metric. You can’t take action on a measurement. Take wait time. Say an issue comes into the backlog and sits there for a long period of time. The organization can improve that wait time by taking it out of the backlog and deprioritizing it, or they can move smaller issues out of backlog faster by letting the bigger, non-priority items sit. “So I can say, traditionally, this team has a high defect ratio. That would be a metric to me,” Knight said. “What are they doing wrong? Now we can go in and look at that with a subjective point of view, of ‘I’m trying to help them. Maybe they have the wrong skills; maybe the team is misaligned.’ You can start to take action on the metrics.”
Using metrics also allows organizations to actually measure if they’re improving their processes. Removing waste will show a decrease in time to deliver and the average time to deliver will improve. But, without metrics, if you remove that piece of waste, you only get a measurement that says it has taken less time to deliver. From that, an organization could extrapolate that it’s improving its processes, but there is no measurable proof that it has had that impact.
Then there are KPIs. Having looked at its systems and making changes against metrics that have been collected, an organization can, for example, see that its throughput has increased by 10 percent. That is a KPI. From there, the organization can look in and see that more defects are coming back, and further see that is the result of a new team using better testing practices and catching more problems.
Knight said, “It’s going to take me a variable amount of time to fix individual defects. But perhaps I come up with a quicker process for finding the defects, which results in faster remediation. I’ve found a different way, a better way to do that.. So you use metrics to understand and improve your processes.”
And that’s what value stream integration does to make you more predictable.
Content provided by SD Times and ConnectALL